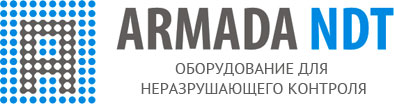
Неразрушающий контроль в атомной энергетике. Требования к проведению контроля металла и сварных соединений. Часть 1
НК за состоянием металла и сварных соединений оборудования и трубопроводов в процессе изготовления, монтажа и эксплуатации выполняется в соответствии с требованиями федеральных Правил Госатомнадзора России, а именно:
- ОПБ-88/97 "Общие положения обеспечения безопасности атомных станций";
- ПНАЭ Г-7-008-89 "Правила устройства и безопасной эксплуатации оборудования и трубопроводов атомных энергетических установок";
- ПНАЭ Г-7-010-89 "Сварные соединения и наплавки. Правила контроля".
- В развитие требований федеральных Правил разработана серия документов, устанавливающих технологию методов НК, требования к аппаратуре и средствам контроля, а также к дефектоскопическим материалам:
- ПНАЭ Г-7-014-89 "Унифицированные методики контроля основных материалов (полуфабрикатов), сварных соединений и наплавки оборудования и трубопроводов атомных энергетических установок. Ультразвуковой контроль. Часть 1. Контроль основных материалов (полуфабрикатов);
- ПНАЭ Г-7-015-89 "То же. Магнито-порошковый контроль";
- ПНАЭ Г-7-016-89 "То же. Визуальный и измерительный контроль";
- ПНАЭ Г-7-017-89 "То же. Радиографический контроль";
- ПНАЭ Г-7-018-89 "То же. Капиллярный контроль",
- ПНАЭ Г-7-019-89 "То же. Контроль герметичности. Газовые и жидкостные методы";
- ПНАЭ Г-7-030-91 "То же. Ультразвуковой контроль. Часть 2. Контроль сварных соединений и наплавки";
- ПНАЭ Г-7-031-91 "То же. Ультразвуковой контроль. Часть 3. Измерение толщины монометаллов, биметаллов и антикоррозионных покрытий";
- ПНАЭ Г-7-032-92 "То же. Ультразвуковой контроль. Часть 4. Контроль сварных соединений из стали аустенитного класса".
Дополнительные требования поконтролю качества оборудования и трубопроводов могут отражаться также при изготовлении, монтаже и ремонте в конструкторской документации (КД), а при эксплуатации – в типовых и рабочих программах.
В случае необходимости проведения НК конкретных компонентов АЭС или их узлов, что особенно актуально при эксплуатации, допускается проведение контроля по методическим инструкциям, разработанным на основе унифицированных методик. На применение упомянутых инструкций должно быть получено разрешение Госатомнадзора России.
Классификация объектов контроля
В зависимости от степени влияния на безопасность АЭС оборудование и трубопроводы системы, составной частью которой они являются, подразделяются на группы А, В и С.
В группу А входят оборудование и трубопроводы, разрушение которых является исходным событием, приводящим к превышению установленных для проектных аварий пределов повреждения твэлов при проектном функционировании систем безопасности, а также корпуса реакторов и технологических каналов любых АЭУ независимо от последствий их разрушения.
В группу В входят оборудование и трубопроводы, разрушение которых приводит к неустранимой штатными запорными органами утечке теплоносителя, обеспечивающего охлаждение активной зоны реактора, и/или требует введения в действие систем безопасности, а также оборудование и трубопроводы систем АЭУ с реакторами на быстрых нейтронах, работающие в контакте с жидкометаллическим теплоносителем независимо от последствий их разрушения (за исключением оборудования и трубопроводов, относящихся в группе А).
В группу С входят:
1) не вошедшие в группу А и В оборудование и трубопроводы, разрушение которых приводит к утечке теплоносителя, обеспечивающего охлаждение активной зоны реактора;
2) оборудование и трубопроводы, разрушение которых приводит к выходу из строя одного из каналов системы безопасности;
3) оборудование и трубопроводы, разрушение которых приводит к выходу высоко- или средне-активных радиоактивных сред.
Конкретная номенклатура оборудования и трубопроводов с указанием их принадлежности к группам А, В и С устанавливается конструкторскими и проектными организациями на чертежах общих видов оборудования или сборочных чертежах, а также на сборочных чертежах трубопроводов и согласовывается с Госатомнадзором России.
В зависимости от группы оборудования и условий работы устанавливаются три категории сварных соединений, определяющие объем и нормы оценки качества:
I категория - сварные соединения оборудования и трубопроводов группы А;
II категория - те же группы В, работающие постоянно или периодически в контакте с радиоактивным теплоносителем;
III категория - те же группы В, не работающие в контакте с радиоактивным теплоносителем, а также те же группы С.
В зависимости от рабочего давления сварные соединения II и III категорий подразделяются на подкатегории IIа, IIв, IIIа, IIIв и IIIc, работающие под давлением:IIа - свыше 5 МПа; IIв - до 5 МПа; IIIа - 5 МПа; IIIв - свыше 1,7 МПа до 5 МПа включительно; IIIc - до 1,7 МПа и ниже атмосферного.
Категории сварных соединений назначаются конструкторской организацией и указываются в конструкторской документации.
Объем, периодичность и методы НК
Объем, периодичность и методы НК основного металла и сварных соединений оборудования и трубопроводов регламентируются федеральными Правилами.
При эксплуатации эти требования конкретизируются типовыми программами, разработанными эксплуатирующими организациями, например: "Типовая программа эксплуатационного контроля за состоянием основного металла и сварных соединений оборудования и трубопроводов систем, важных для безопасности, энергоблоков с РБМК-1000 Курской и Смоленской АЭС" АТПЭ-10-96; "Типовая программа эксплуатационного контроля за состоянием основного металла и сварных соединений оборудования и трубопроводов атомных электростанций с ВВЭР-1000" АТПЭ-9-97; и другие.
При этом обязательному контролю подлежат:
- оборудование группы А (корпуса реакторов) - сварные соединения, антикоррозионные наплавки, основной металл в зонах концентрации напряжений и зонах, расположенных напротив активной зоны, сварные соединения и радиусные переходы патрубков присоединения трубопроводов, уплотнительные поверхности разъемных соединений корпусов и крышек, сварные швы присоединения опор, шпильки, металл в резьбовых отверстиях под шпильки, опорные бурты нажимных колец и другое оборудование группы А;
- оборудование группы В - все сварные соединения корпусов и основной металл в зонах концентрации напряжений, швы приварки патрубков к корпусу и крышке, сварные швы коллекторов или трубных досок парогенераторов, внутренняя поверхность корпусов в зоне пар-вода, радиусные переходы патрубков, зоны перемычек между отверстиями в корпусе, сварные швы присоединения опор, болты и шпильки, металл в резьбовых отверстиях под болты и шпильки;
- трубопроводы группы В - сварные соединения и антикоррозионные наплавки труб и коллекторов, гибы, сварные швы приварки патрубков и труб в местах отводов, сварные швы тройников, переходов, присоединения опор.
Необходимость и объем контроля оборудования и трубопроводов группы С устанавливается конструкторской (проектной) организацией.
НК основного металла и сварных соединений
НК состояния металла и сварных соединений проводится при изготовлении и монтаже с целью
- выявления в основном металле и сварных соединениях изготавливаемых (монтируемых) оборудования и трубопроводов недопустимых действующими Правилами и/или конструкторской документацией несплошностей (дефектов) и последующего их устранения (ремонта);
- фиксации показаний различно ориентированных в основном металле и сварных соединенях допустимых поверхностных и объемных несплошностей. Эти показания заносятся в паспорта поставляемых (монтируемых) на АЭС оборудования и трубопроводов и используются при анализе состояния металла и сварных соединений в процессе эксплуатации;
а также при эксплуатации с целью:
- выявления и фиксации поверхностных и объемных (внутренних) дефектов (несплошностей), ориентированных в различных пространственных направлениях в основном металле и сварных соединениях ;
- оценки состояния металла. Контроль состояния металла и сварных соединений при эксплуатации подразделяется на предэксплуатационный, периодический и внеочередной.
- Предэксплуатационный контроль проводится до начала эксплуатации, периодический - в процессе эксплуатации в следующие сроки:
- первый - не позднее 20000 ч с начала работы оборудования и трубопроводов;
- последующие - для оборудования группы А и оборудования и трубопроводов группы В, изготовленных из труб и обечаек с продольными сварными швами, не позднее, чем через каждые 30000 ч работы, отсчитываемых от даты предыдущего контроля;
- для остального оборудования и трубопроводов, подлежащих контролю - через каждые 45000 ч.
Внеочередной контроль проводится:
1) после землетрясения, соответствующего по бальности проектному или превышающему его;
2) при нарушении нормальных условий эксплуатации или в аварийных ситуациях, приведших к изменению параметров работы оборудования и трубопроводов до уровня, превышающего расчетный;
3) по решению руководства предприятия-владельца оборудования и трубопроводов или местного органа Госатомнадзора России.
Контроль за целостностью основного металла и сварных соединений на всех этапах изготовления, монтажа и эксплуатации оборудования и трубопроводов осуществляется неразрушающими методами. При этом применяются:
- визуальный и измерительный контроль;
- капиллярный контроль;
- магнитопорошковый контроль;
- ультразвуковой контроль;
- радиографический контроль;
- контроль герметичности.
Другие методы контроля могут быть применены в случаях, предусмотренных конструкторской документацией или регламентированных типовой программой контроля, при наличии утвержденных в установленном порядке методических инструкций по контролю и правил их применения.
Ультразвуковой контроль основного металла и сварных соединений проводится по ПНАЭ Г-7-014-89 и ПНАЭ Г-7-030-91 соответственно.
При настройке чувствительности для контроля сварных соединений устанавливаются следующие уровни:
а) браковочный, при котором проводится оценка допустимости обнаруженной несплошности по амплитуде эхо-сигнала. Браковочный уровень (максимально допустимая эквивалентная площадь) определяется ПНАЭ Г-7-010-89;
б) контрольный, при котором проводятся измерение характеристик обнаруженных несплошностей и оценка их допустимости по предельным значениям характеристик (условной протяженности, высоте и др.). Контрольный уровень (наименьшая фиксируемая эквивалентная площадь) выше браковочного на 6 дБ;
в) поисковый, при котором проводится поиск несплошностей. Поисковый уровень выше контрольного не менее, чем на 6 дБ. Чувствительность при контроле основного металла определяется из заданного в ТУ уровня фиксации через эквивалентную площадь (или диаметр) плоскодонного отверстия, либо искусственного отражателя в виде риски (при контроле труб). Поисковая чувствительность устанавливается на 6 дБ выше уровня фиксации.
Оборудование для ручного ультразвукового контроля, используемое на заводах-изготовителях, в монтажных организациях и на АЭС - это, прежде всего, серийно выпускаемые ультразвуковые дефектоскопы марки УД-2-12 с комплектом пьезопреобразователей. Замеры толщины проводятся ультразвуковыми толщиномерами марки УТ-93П, Кварц-6.
Применяются также импортные приборы, например, дефектоскоп иЗЫ50 и иЗЫ52 фирмы "Крауткремер" и толщиномеры марки 0М401_ той же фирмы.
Радиографический контроль проводится в соответствии с ПНАЭ Г-7-017-89.
При радиографическом контроле на всех этапах изготовления, монтажа и эксплуатации оборудования применяются рентгеновские аппараты, в том числе и импульсные, а также такие источники тормозного рентгеновского излучения, как линейные ускорители, микротроны, бетатроны. Кроме того, используются также и радионуклидные источники для гамма-дефектоскопии (75Sе, 192Ir, 60Co и ряд других). В качестве детектора излучения применяются отечественные радиографические пленки типа РТ-1, РТ-4М, РТ-4Ш, РТ-5. Допускается применение импортных пленок с аналогичными характеристиками, например таких, как пленки фирмы "Агфа-Геварт" (Бельгия) 02, 04, 05, 07, 08, 010.
Использование других источников излучений и радиографических пленок разрешается только по согласованию со специализированной организацией.
Чувствительность контроля устанавливается по радиационной толщине (суммарная длина участков оси рабочего пучка направленного первичного ионизирующего излучения в материале контролируемого объекта).
При просвечивании через две стенки (или более) чувствительность контроля устанавливается по суммарной номинальной толщине этих стенок.
Радиографический контроль следует выполнять через одну стенку с использованием рентгеновского излучения. Гамма-просвечивание и контроль через две стенки применяются только в случае технической невозможности или возникновения технических трудностей, например, из-за ограничения доступа при монтаже и эксплуатации.
Цветная дефектоскопия (капиллярный контроль), выполняемая по ПНАЭ Г-7-018-89, позволяет обнаруживать дефекты, выходящие на поверхность: трещины, поры, раковины, непровары, межкристаллитную коррозию и другие несплошности.
При проведении капиллярного контроля применяется аппаратура в соответствии с ГОСТ 18442-80, источники освещения контролируемой поверхности, приборы для контроля освещенности контролируемой поверхности, контрольные образцы.
В дефектоскопических материалах, используемых при капиллярном контроле сварных соединений из аустенитных сталей или сплавов на железо- никелевой основе, содержание хрома и серы в сухом остатке, полученном после выпаривания 100 г материала (пенетранта), не должно превышать 1 % для каждого из указанных элементов.
Применение новых наборов дефектоскопических материалов согласовывается со специализированной организацией.
При капиллярном контроле при изготовлении, монтаже и эксплуатации оборудования и трубопроводов применяют дефектоскопические наборы, обеспечивающие выявление дефектов по второму классу чувствительности (ПНАЭ Г-7-018-89).
Магнитопорошковый контоль. В зависимости от размеров выявляемых несплошностей и шероховатости контролируемой поверхности унифицированной методикой ПНАЭ Г-7-015-89 устанавливается три условных уровня чувствительности (А, Б и В), определяемых минимальной шириной и протяженностью условных дефектов.
При этом под условным дефектом понимается поверхностный дефект в виде плоской щели с параллельными стенками, ориентированный перпендикулярно к контролируемой поверхности и направлению магнитного поля и соотношением глубины к ширине равным 10.
Для магнитного контроля используются универсальные (переносные) и специализированные магнитопорошковые дефектоскопы; источники освещения контролируемой поверхности; приборы для измерения напряженности магнитного поля и тока, а также измерения концентрации магнитной суспензии, освещенности и шероховатости контролируемой поверхности; контрольные образцы; различные вспомогательные приспособления.
Визуальный и измерительный контроль проводится по ПНАЭ Г-7-016-89 невооруженным глазом (допускается применение луп с увеличением до семикратного) с помощью измерительных инструментов и приборов.
Для измерительного контроля следует применять приборы и инструменты, класс точности которых обеспечивает надежное определение измеряемых величин с погрешностью не более регламентированной ПНАЭ Г-7-016-89 или конструкторской документацией.
При измерениях используют: линейки мерительные металлические по ГОСТ 427-75, микрометры, штангенциркули по ГОСТ 166-89, рулетки измерительные металлические по ГОСТ 7502-89, индикаторы по ГОСТ 577-68, лупы измерительные по ГОСТ 25706-83 и другие приборы и инструменты.
Допускается применение зеркал, перископов, волоконных световодов и телекамер при условии обеспечения выявления дефектов, регламентированных федеральными Правилами.
Требования к средствам
контроля и материалам для дефектоскопии
Для контроля следует применять установки и аппаратуру, которые должны отвечать требованиям соответствующих государственных стандартов, унифицированных методик и инструкций по эксплуатации.
Допускается применение других установок и аппаратуры (например, полученных по импорту), при условии, что их применение обеспечивает выполнение всех требований Правил и конструкторской документации по контролю сварных соединений и наплавленных деталей.
Проверка состояния установок и аппаратуры для контроля проводится периодически по графику, составленному в соответствии с указаниями правил технической эксплуатации этих установок и аппаратуры, паспортов и инструкций. Сведения о периодических поверках и контролируемых параметрах вносятся в соответствующие разделы паспортов (формуляров) на установки и аппаратуру и оформляются актом.
Метрологическое обеспечение осуществляется в соответствии с требованиями госстандартов России: на установки и аппаратуру, отнесенные к средствам измерения, оформляется сертификат утверждения типа измерения, а на не являющиеся средствами измерения - сертификат соответствия.
Каждая партия материалов для дефектоскопии (порошков, пенетрантов, пленки, реактивов и т. п.) контролируется на
- наличие на каждом упаковочном месте (пачке, коробке, емкости) этикеток (сертификатов и др.) с проверкой полноты приведенных в них данных и соответствия этих данных требованиям стандартов или технических условий на контролируемые материалы;
- отсутствие повреждений и порчи упаковки или самих материалов;
- срок годности;
- соответствие качества материалов требованиям методических документов на данный метод контроля.
Автоматизированный контроль
Ручной НК имеет ряд недостатков. В первую очередь, это низкие производительность и достоверность контроля, недостаточное документирование результатов, значительное влияние человеческого фактора, а при эксплуатации - еще и большие дозовые нагрузки персонала.
Автоматизированный или полуавтоматизированный контроль, используемый, как правило, в процессе эксплуатации, частично или полностью устраняет указанные недостатки.
Для эксплуатационного контроля корпусов реакторов ВВЭР-440 и ВВЭР-1000 применяется отечественное и импортное оборудование.
Оборудование для автоматизированного контроля корпуса реактора:
- УСК-213 - унифицированная система контроля корпуса реактора В-213 (ВВЭР-440) снаружи (ультразвуковой и телевизионный контроль) с подсистемами: 01 - ультразвукового контроля цилиндрической части корпуса и днища, 02 - телевизионного перископического осмотра внутренней поверхности корпуса реактора, 03 - ультразвукового контроля сварных швов корпуса в зоне патрубков и основного металла и сварных швов приварки переходных втулок ДуS00 и Ду2S0;
- СК-187 - передвижная система контроля корпуса реактора ВВЭР-1000 снаружи с подсистемами: 01 - внешнего телевизионного и ультразвукового контроля цилиндрической части корпуса и днища, 02 - ультразвукового контроля сварных швов корпуса в зоне патрубков и основного металла патрубков Ду8S0, а также ультразвуковой контроль основного металла патрубков САОЗ и швов приварки этих патрубков к корпусу;
- СК-187.04 - система внутреннего ультразвукового и телевизионного контроля корпусов ВВЭР (Нововоронежская АЭС);
- автоматизированные системы контроля корпусов реактора ВВЭР-440 и ВВЭР-1000 фирмы Сименс (Германия) - на Кольской АЭС, а также ряд других автоматизированных ультразвуковых, вихретоковых и телевизионных систем контроля различных компонентов АЭС поставки зарубежных фирм: Технатом (Испания) - на Кольской и Ленинградской АЭС, Марубени (Япония) - на Ленинградской АЭС, Альстом (Германия) на Нововоронежской АЭС и др.
Методологические требования отражаются в методиках (технологиях) автоматизированного контроля, разрабатываемых применительно к конкретным средствам автоматизированного контроля. В частности, такие требования содержатся в следующих документах:
- СК 187 М.00.00.00.00.00 Д1 "Система контроля корпусов реакторов ВВЭР-1000. Методика автоматизированного ультразвукового контроля";
- СК 187.04.00.00.00.00 Д "Система внутреннего контроля корпусов ВВЭР. Методика ультразвукового контроля";
- "УСК-213.00.00.00.00 Д. Методика ультразвукового контроля" и др.
Оценка результатов эксплуатационного контроля
При оценке состояния основного металла и сварных соединений оборудования и трубопроводов АЭС используется приведенная на рис. 1 схема принятия решений, содержащая типовые мероприятия, выполняемые при проведении такой оценки.
Принятые определения
Уровень фиксации (записи) - порог, начиная с которого показатели эксплуатационного контроля металла (ЭКМ) должны документироваться (входить в отчеты по контролю). Все показатели ЭКМ, лежащие выше уровня фиксации, анализируются и сравниваются с предыдущими результатами ЭКМ.
Показатели ЭКМ - данные по нарушению сплошности металла, нарушению его структуры или других характеристик, определяемые методами эксплуатационного контроля; могут выражаться в условных параметрах (например, эквивалентная площадь отражателя или условная протяженность несплошности по результатам ультразвукового контроля) или физических единицах (например, геометрических размерах).
Несплошность - нарушение сплошности металла, нарушение структуры или других характеристик металла, определяемые методами НК, допустимое отклонение от требований, установленных действующими Правилами или другими нормативными документами, регламентирующими нормы оценки качества сварных соединений и основного металла трубопроводов и оборудования АЭС.
Дефект - недопустимое отклонение от требований, установленных действующими правилам или другими нормативными документами, регламентирующими нормы оценки качества сварных соединений и основного металла оборудования и трубопроводов АЭС.
Браковочный уровень - максимально допустимое показание результатов несплошности, регламентированное Правилами или другими нормативными документами, устанавливающими нормы оценки качества сварных соединений и основного металла оборудования и трубопроводов АЭС.
Подэтап 00 - проведение ЭКМ согласно требованиям Типового регламента.
Подэтап 01 - регистрация (протоколы, акты) показателей ЭКМ, выполняемого в соответствии с требованиями Типовой программы контроля.
Подэтап 02 - оценка результатов ЭКМ, превышающих контрольный уровень.
Подэтап 03 - выявление новых не- сплошностей по сравнению с результатами предыдущего ЭКМ (если новых несплошностей не возникло, то проводится анализ изменения показаний зафиксированных ранее несплошностей).
Подэтап 04 - выявление изменений показаний несплошностей, зафиксированных в предыдущий ЭКМ (если выявлено изменение показаний, то необходимо оценить величину прироста и сделать заключение относительно причин и времени этих изменений - под- этап 05).
Подэтап 05 - оценка допустимости показаний несплошности и/или ее прироста (сравнение показаний несплош- ностей и зафиксированных ранее дефектов с браковочными уровнями), выявление дефектов, а также оценка допустимости возникновения новых или прироста показаний зафиксированных ранее несплошностей.
Подэтап 06 - проведение уточненного (экспертного) ЭКМ, если показания появились в первый раз или есть увеличение показателей состояния, чтобы можно было сделать заключение о виде, положении и величине несплошности или дефекта и предположительно о причинах их появления.
Подэтап 07 - если несплошность превышает допустимые пределы норм оценки качества металла в эксплуатации и определяется как дефект, проводится расследование с оформлением акта обследования дефектного узла, и для принятия решения по результатам контроля назначается комиссия.
В состав комиссии входят представители эксплуатирующей организации, АЭС, инспектор Госатомнадзора России, а при необходимости - представители специализированной организации, проектной (конструкторской) организации и завода-изготовителя (монтажной организации).
При работе комиссии проводятся:
- повторный (экспертный) контроль имеющимися приборами,в том числе с использованием средств дефекто- метрии для уточнения геометрических характеристик несплошности/ дефекта, а также контроля аналогичных мест и узлов с аналогичными условиями работы;
- анализ материалов поверочного расчета на прочность в соответствии с требованиями Норм расчета на прочность, а при его отсутствии - выполнение соответствующего поверочного расчета на прочность;
- оценка допустимости дефектов металла по результатам НК: расчет допускаемых дефектов в металле оборудования и трубопроводов во время эксплуатации АЭС проводится методами механики разрушения.
Результаты работы комиссии, отчетные документы о проведенном контроле и предлагаемые решения направляются в эксплуатирующую организацию, проектную (конструкторскую) организацию и Госатомнадзор России.
Подэтап 08 - принятие комиссией специального решения на основании проведенного расследования.
Подэтап 09 - по результатам расследования определяется возможность допуска узла с выявленной несплошностью в эксплуатацию при условии исключения причин ее возникновения и проведения дополнительных мероприятий.
Подэтап 10 - принятие комиссией решения по результатам контроля о возможности дальнейшей эксплуатации узла.
Подэтап 11 - принятие комиссией решения о необходимости устранения выявленного дефекта (ремонта узла) и/или замены элемента.
Специальные решения, принятые комиссией, оформляются техническим решением, которое составляется АЭС, утверждается эксплуатирующей организацией и согласовывается с Госатомнадзором России.
Рис. 1. Схема оценки допустимости дефекта по результатам НК
Подэтап 12 - исключение причин возникновения дефекта, дополнительные работы (например, установка измерительной аппаратуры, сокращение интервалов контроля, увеличение объемов контроля, изменение, при необходимости, условий эксплуатации отремонтированного узла или замененного компонента).
Подэтап 13 - проведение базового (предэксп-луатационного) контроля после замены или ремонта узла (перед пуском его в эксплуатацию).
Подэтап 14 - проведение технического освидетельствования и принятие комиссией решения по результатам контроля при участии инспектора Госатомнадзора России.
Разрешение на пуск и дальнейшую эксплуатацию оборудования выдается Госатомнадзором России после представления материалов по обследованию, решения о мерах по устранению дефектов, сдаточной документации по ремонту, решения об отступлении от установленных требований с обоснованием возможности дальнейшей безопасной эксплуатации.