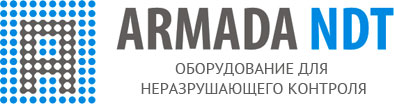
Автоматизированные установки магнитопорошкового контроля концов и торцов труб
Об авторе
Ершов Сергей Гениевич
Директор ЗАО «Виматек», канд. физ-мат. наук, доцент, II уровень по магнитопорошковому и капиллярному методам контроля, специалист в области физики поверхности твердого тела.
Начало третьего тысячелетия в нашей стране характеризуется заметным подъемом производства во многих отраслях промышленности, в том числе - производства труб различного сортамента, включая нефтяные и газовые. Но, в отличие от советского периода, сегодня к производству труб предъявляются иные требования, и это касается, прежде всего, качества производимой продукции.
Тело трубы контролируется ультразвуковым, рентгеновским и другими методами. Наиболее высокие требования предъявляются к контролю качества концов и торцов труб, поскольку именно в этих областях при сварке труб и в процессе эксплуатации трубопроводов концентрируются механические напряжения и деформации. Микроскопические трещины и расслоения, выходящие на поверхность и не оказывающие никакого влияния на потребительские свойства тела трубы, в напряженном состоянии металла увеличиваются в размерах и вызывают постепенное разрушение трубопровода. Поэтому сегодня на трубопрокатных заводах заметен повышенный интерес к методам контроля концов и торцов труб разного диаметра. Цель статьи - помочь специалистам соответствующих производств в какой-то мере восполнить существующий дефицит информации по этому вопросу.
При контроле качества концов и торцов труб необходимо выявлять микродефекты, которые столь малы, что они не могут быть обнаружены ни рентгеновским, ни ультразвуковым методами. Поэтому применяется самый чувствительный метод - магнитопорошковая дефектоскопия. Этот метод включает в себя намагничивание объекта контроля и нанесение на его поверхность цветных или люминесцентных магнитных частиц малого размера, взвешенных в различных средах. Дефект, находящийся на поверхности или в подповерхностной области, создает градиент магнитного поля, приводящий к скоплению магнитных частиц в области дефекта. Визуальное наблюдение скоплений частиц на поверхности объекта контроля позволяет обнаружить дефекты. Чувствительность метода настолько высока, что могут быть обнаружены трещины с шириной раскрытия, составляющей доли микрона и длиной менее миллиметра. Если ориентация дефекта параллельна вектору намагниченности, то градиент поля крайне мал и дефект не обнаруживается. Поэтому контролируемый объект намагничивают в двух взаимно перпендикулярных направлениях. Это обеспечивает нахождение нарушений любой ориентации. В классическом варианте метод носит визуальный, качественный характер, а достоверность и качество контроля полностью определяются компетентностью и личными качествами дефектоскописта.
Рассмотрим основные технические решения по установке для контроля концов и торцов труб.
Первый вариант обеспечивает поперечное намагничивание конца трубы с помощью селеноида (рис. 1с), а циркулярное намагничивание - электродом, пропущенным внутрь трубы. Ток циркулярного намагничивания протекает по электроду, стенке трубы и наружному электроду, т.е. через два прижимных контакта к стенке трубы. Эту схему целесообразно использовать при контроле труб небольшого диаметра, поскольку с увеличением размеров трубы требуются большие токи намагничивания, что сопряжено с опасностью образования «прижогов» в местах контактов трубы с электродами. Несомненным достоинством этого варианта является возможность использования как переменного, так и постоянного токов намагничивания для контроля поверхностных и подповерхностных дефектов.
Второй вариант схематически представлен на рис. 1б. Около торца трубы вращается подковообразный постоянный магнит (патент № 34017). Такой способ реализует условия вращающегося вектора намагниченности в околоторцевой области материала трубы, что позволяет одновременно регистрировать дефекты любой ориентации. Вращение трубы вокруг своей оси дает возможность последовательно контролировать всю поверхность торца независимо от диаметра трубы и делает возможным контроль труб любого диаметра. К недостаткам такого метода относятся: невозможность регулировать напряженность намагничивающего поля (кроме как изменением расстояния между магнитом и трубой); контроль только торцов трубы и различные значения поля для намагничивания вдоль и поперек стенки трубы. Последнее обстоятельство особенно негативно для достижения одинаково оптимальных условий выявляемое дефектов во всех направлениях.
Заметным шагом вперед явилось использование в этих установках цветной высокоразрешающей видеокамеры для наблюдения за состоянием поверхности торца трубы и выявления индикаций. Это позволяет оператору покинуть место непосредственного контроля, сопряженного с опасностью травматизма при вращении трубы, а также использовать оптическую систему видеокамер для увеличения контролируемой области до геометрических размеров, при которых самые мелкие дефекты становятся легко различимы. Однако, несмотря на использование оптико-электронных средств наблюдения за состоянием поверхности, магнитопорошковый метод в этой установке остался визуальным, т. е. роль дефектоскописта в процессе контроля сохранилась доминирующей.
Влияние оператора-дефектоскописта, его квалификации на результат визуального контроля - иными словами роль человеческого фактора - очень важна. Это существенно сдерживает развитие любого метода. Действительно, оператор непрерывно, в течение нескольких часов, должен напряженно всматриваться в индикаторный рисунок, созданный магнитными частицами на поверхности
объекта контроля. Особенно велико напряжение, когда выявляются мелкие дефекты. Естественно, что от оператора требуется предельная концентрация внимания, зрения и «шестого чувства», и находиться в таком состоянии в течение длительного времени - задача трудновыполнимая. Монотонно выполняемая операция быстро рассеивает внимание, и возникает большая вероятность пропустить дефект, снижается достоверность контроля. Радикальное решение этой проблемы - использование программ автоматического поиска дефектов.
Рис. 1. Варианты схем намагничивания концов и торцов труб: а - с использованием селеноида и внутреннего электрода; б - с вращающимся постоянным магнитом; в - с ортогональными магнитопроводами с независимой регулировкой магнитного поля
Не менее актуальным является автоматический контроль важнейших параметров установки: интенсивности ультрафиолетового источника, степени затененности области контроля от внешнего света, качества суспензии и т.д.
Стандарты на магнитопорошковый контроль требуют проверки этих параметров, например, перед началом каждой смены (а что будет с контролем, если, например, интенсивность источника УФ излучения изменится в середине смены?). На практике операторы чаще полагаются на свой опыт и внешние признаки, чем на показания приборов, и это ставит под сомнение результаты контроля и их надежность.
Рис. 2. Схема автоматизированной установки магнию порошкового контроля
Вариант полностью автоматизированной установки разработан фирмой «Виматек» - совместным российско-чешским предприятием (с чешской стороны - признанный лидер магнитопорошкового метода - компания АТС). В качестве намагничивающего элемента использованы ортогонально расположенные магнитопроводы с катушками намагничивания и независимым регулированием тока в них (рис. 1в). Один из магнитопроводов охватывает стенку трубы на некоторую длину, намагничивая не только торец, но и конец трубы. Этим и независимым регулированием токов намагничивания ликвидируются недостатки метода вращения постоянного магнита, но сохраняются преимущества последовательного контроля конца трубы большого диаметра по периметру при вращении трубы вокруг своей оси.
Рассмотрим работу установки более детально. Труба поднимается на пово-ротно-подъемных роликах в позицию контроля (рис. 2). С обоих концов к трубе по направляющим подъезжают две тест- станции, каждая из которых состоит из механических узлов перемещения станции и ее позиционирования, электроники управления электро- и пневмоприводами, силовой электроники формирования токов намагничивания, ультрафиолетового источника, затемненного экрана, системы орошения концов труб магнито- порошковой суспензией, видеокамерами наблюдения. Каждая станция работает автономно в автоматическом режиме по следующему алгоритму.
Система автоматического слежения позиционирует тест-станцию на определенном расстоянии от конца трубы. Датчики УФ излучения и видимого света контролируют затемненность места контроля и интенсивность УФ излучения. Проверяется наличие люминесцентной жидкости и ее качество (принцип проверки качества зависит от свойств суспензии и включает, как правило, измерение двух параметров). Люминесцентная жидкость циркулирует по двум контурам - контуру перемешивания, активному перед началом работы и между циклами контроля, и контуру орошения места контроля, активному при работе. Датчики магнитного поля, расположенные в зоне контроля и включенные в систему поддержания токов намагничивания, обеспечивают идентичные условия намагничивания. По спектральному составу видеосигнала определяются оптимальные условия оптической фокусировки видеокамер, при необходимости осуществляется автоматическое управление микродвигателями объектива камеры. Сигнал разрешения контроля торца и конца трубы выдается, если ни одна из перечисленных величин не выходит за допустимые пределы. Если программа управления обнаружит недопустимые отклонения от требуемых значений, то процесс контроля будет приостановлен, и на экран дисплея оператора будет выдано сообщение об ошибке.
Далее труба намагничивается, поливается суспензией и поворачивается вокруг своей оси для контроля по всему периметру. Видеоизображение контролируемой области поступает на процессор обработки изображения с установленной программой автоматического поиска дефектов.
Суть программы - в компьютерной обработке изображения, основанной на вычислении градиентов контрастности видеосигнала по различным направлениям, построении топологически связанных областей поверхности и фильтрации изображения от структурных элементов, которые считаются априорно известными (заметим, однако, что технические решения проблемы автоматического поиска не так просты и очевидны, как собственно формулировка задачи). Программа допускает настройку на поиск дефектов с заданными параметрами или их превышающими, например, по длине дефекта, его площади, количеству дефектов на единицу площади и т.д.
При нахождении таких дефектов программа выводит дефектное изображение на экран монитора, приостанавливает процесс контроля и звуковым сигналом оповещает оператора, который тщательно изучает подозрительное место и принимает окончательное решение о годности трубы. При этом оператор не работает в рутинном утомительном режиме непрерывного контроля, он занимается изучением только тех немногих участков поверхности трубы, на которые программа обратила его внимание (для принятия адекватного решения оператор может многократно увеличить изображение дефектной области, улучшить его разнообразными фильтрами, записать в базу данных или воспользоваться базой данных для сравнения и т.д.). В этом случае вероятность пропустить дефект становится исчезающе мала. Имея компьютерное изображение подозрительного фрагмента трубы, оператор всегда может получить любую консультацию, воспользовавшись электронными средствами связи (вплоть до консультаций у заказчика труб).
Если программа не обнаруживает дефектов, то установка работает по заданной программе, контролируя последовательно одну трубу за другой без участия оператора. Команды на окончание контроля одной трубы и начало контроля другой вырабатываются внутри программы. Если обнаруживается подозрительное место, то выполнение программы может быть приостановлено до решения оператора о качестве трубы, или подозрительное место может быть автоматически записано в базу данных, труба промаркирована, и контроль продолжен. Решение о пригодности трубы в этом случае принимается позднее, после анализа записей изображений.
Автоматические системы поиска обладают важнейшей перспективной особенностью: они способны сигнализировать о том, что дефекты присутствуют, даже если их размеры меньше допустимых. Это позволяет вносить коррективы в процесс производства еще до стадии возникновения брака.
Подводя итог, подчеркнем, что применение систем видеонаблюдения контролируемой области позволяет исключить риск, связанный с нахождением дефектоскописта вблизи вращающейся трубы, а также увеличить геометрические размеры контролируемой области так, чтобы мелкие дефекты легко различались. Использование системы улучшения и архивирования индикаторных изображений, совмещенной с системой поиска и расшифровки дефектов, исключает влияние человеческого фактора на качество контроля. А применение системы контроля важнейших параметров установки повышает достоверность и однозначность результатов контроля.