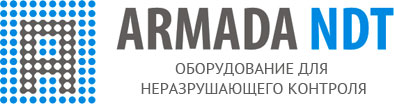
Современные возможности и тенденции развития акустико-эмиссионного метода
Об авторах
Гуменюк Владимир Алексеевич
Начальник сектора технической диагностики ГНЦ ЦНИИ им. акад. А. Н. Крылова, к. т. н.
Сульженко Виктор Алексеевич
Яковлев Александр Викторович
Научные сотрудники ГНЦ ЦНИИ им. акад. А. Н. Крылова, II уровень по акустическим методам контроля
Акустико-эмиссионный (АЭ) метод - один из наиболее молодых и динамично развивающихся методов технической диагностики. Его физическая сущность заключается в регистрации расставленными по поверхности контролируемой конструкции акустическими датчиками - преобразователями акустической эмиссии (ПАЭ)
- дискретных волн разгрузки, вызванных локальной структурной перестройкой материала при его деформировании и локальном разрушении (пластические деформации, скачкообразное развитие трещины).
Основные достоинства метода заключаются в возможности:
- дистанционного интегрального контроля состояния крупногабаритного объекта, включая возможность одновременного контроля нескольких разнопрофильных объектов;
- выявления опасных (развивающихся) дефектов, причем в районах конструкции, недоступных никаким другим методам НК;
- диагностирования объектов без полной разборки и снятия защитных элементов или изоляции, в том числе при их подводном или подземном залегании.
Если к этому добавить такое качество, как оперативность оценки состояния объекта, то приведенные возможности АЭ-метода ставят его вне конкуренции со всеми известными на сегодня методами НК.
АЭ-метод выступает как самостоятельный, если по его оценке, полученной на основании критериального анализа зарегистрированной АЭ-информации от источников-дефектов, состояние объекта признается удовлетворительным. В противном случае для окончательной оценки привлекаются дополнительные методы НК. Наибольшую надежность оценки дает применение АЭ-метода в комплексе с такими традиционными методами, как визуально-оптический, капиллярный, магнитопорошковый, ультразвуковой, рентгеновский. Эффективность комплексного контроля в этом случае определяется тем, что в задачу АЭ-метода входит выявление АЭ-активных источников и определение их координат или зон их расположения, обеспечивающее многократную минимизацию объемов последующего контроля традиционными методами. Последние дополняют предварительную АЭ- оценку состояния объекта сведениями о геометрических параметрах и степени опасности выявленных дефектов (размерах, форме, ориентации и глубине залегания).
Основные недостатки этого метода как метода пассивного контроля: - необходимость для его реализации деформирования материала контролируемого объекта, поскольку только при этом условии разнообразные дефекты структуры как концентраторы напряжений излучают дискретные акустические волны локальной упругой разгрузки материала;
Поэтому выбор и исполнение режима нагружения объекта АЭ-контроля, гарантирующего инициирование акустической активности дефектов, является одной из наиболее важных методических задач.
- чувствительность к разнообразным помехам, в том числе электромагнитным, радио-, вибрационным, климатическим, акустическим и прочим.
Статистика показывает, что при АЭ-контроле промышленных объектов более 90 % зарегистрированных сигналов относится к акустическим помехам. Поэтому, как никакой другой, АЭ-метод требует тщательной методической отработки для получения положительных результатов.
Основные области реализации, в которых АЭ-метод наиболее апробирован:
- исследования физических закономерностей деформирования и разрушения структуры материалов, включая металлические и композиционные материалы, керамику;
- экспериментальная конструктивно-технологическая отработка с целью повышения ресурса деталей машин, сварных соединений и узлов; оболочечных и прочих корпусных конструкций в составе масштабных и натурных моделей судостроительной, аэрокосмической, атомной, машиностроительной и других отраслей промышленности;
- диагностика состояний оболочечных и прочих корпусных конструкций, а также широкого класса сосудов давления и трубопроводов (как технологических, так и магистральных продуктопроводов) в процессе их гидравлических и пневматических испытаний, включая реакторы риформинга, колонны, теплообменники, ресиверы, автоклавы, котлы и прочее оборудование нефтедобывающей, нефтеперерабатывающей, химической и других отраслей промышленности, а также предприятий теплоэнергетического комплекса;
- диагностика состояний различных емкостей, хранилищ, стационарных и транспортных цистерн и прочего наливного оборудования широкого назначения.
Как показывает тематика докладов на XV Российской научно-технической конференции "Неразрушающий контроль и диагностика", особенно много довольно успешных работ по АЭ-диагностике выполняются в настоящее время в двух последних направлениях.
Основные задачи, решаемые АЭ-методом:
- выявление разнообразных дефектов материала, в том числе развивающихся трещин, коррозионных поражений, мест эрозионного износа с определением их местоположения на контролируемом объекте;
- контроль герметичности корпусных конструкций в режиме течеискания и выявление сквозных дефектов, в том числе свищей, коррозионных проеданий и неплотностей соединений;
- контроль сварных швов непосредственно в процессе сварки и в период остывания;
- выявление районов повышенной напряженности и перегруженности конструкций по регистрации зон локальных пластических деформаций и общей текучести материала.
Широкая область реализации метода и круг выполняемых задач определяет и номенклатуру используемой АЭ-аппаратуры, которую можно условно разделить на специализированные малоканальные приборы и универсальные, как правило, многоканальные АЭ-системы.
Для диагностики крупногабаритных корпусных конструкций применяются, как правило, АЭ-системы. Причем необходимость в них определяется не столько габаритами объекта, сколько требованиями многофункциональности. К примеру, заводской объект типа сосуда давления имеет люки, задвижки, присоединенные технологические трубопроводы и соединительную арматуру, через фланцевые соединения которых при пневматическом или гидравлическом нагружении в процессе АЭ-контроля возможны утечки. Следовательно, к используемой АЭ-аппаратуре, наряду с требованием выявления дефектов и их местоположения (локационная аппаратура), предъявляются и требования выявления утечек с указанием конкретного соединения, имеющего пропуск (аппаратура течеискания). Кроме того, эти испытания проводятся одним циклом нагружения, причем для сохранения ресурса испытываемого объекта максимальная нагрузка, как правило, не превышает более чем на 5 - 10 % рабочую. Учитывая эффект Кайзера, снижающий АЭ-информативность участка нагружения до превышения рабочей нагрузки, вероятность высокой активности источников-дефектов в этих условиях достаточно мала. Поэтому необходимо максимально повышать информативность единичного зарегистрированного сигнала, а, следовательно, стремиться к использованию широкополосных ПАЭ и аппаратуры спектрального анализа.
Таким образом, для повышения достоверности и надежности АЭ-контроля промышленных объектов предпочтительно использование многофункциональной (универсальной) аппаратуры.
Рассмотрим основные тенденции, которые прослеживаются в настоящее время при разработке современных АЭ-систем.
- Принцип независимости приемных каналов,
в отличие от принципа использования жестких локационных антенн, образованных из расставленных на объекте групп ПАЭ (не менее трех в группе), предусматривает возможность произвольного формирования антенн на программном уровне из любой комбинации ПАЭ, зарегистрировавших сигнал от источника.
Прогрессивность этого принципа в том, что он обеспечивает минимальную потерю АЭ-информации, излученной в пределах зоны приема ПАЭ, реализуя затем любой вид локации: плоскостную (не менее трех ПАЭ, принявших сигнал), линейную (при двух ПАЭ, принявших сигнал) и зональную, в случае регистрации сигнала одним ПАЭ.
- Модульный принцип формирования приемных каналов позволяет произвольно наращивать число приемных каналов путем включения в систему дополнительных модулей сбора данных и гибко формировать оптимальные схемы расстановки ПАЭ на объектах контроля в зависимости от их габаритов и конфигурации.
Среди АЭ-систем, использующих описанные выше принципы построения, следует отметить системы SPARTAN,
LOCAN (Physical Acoustics Corporation /РАС/, США); AMS, AMSY (Valien Systeme, Германия); "Малахит АС-6А" и "Малахит АС-12А" (НПФ ДИАТОН и РНЦ "Курчатовский институт") и ряд других.
- Цифровая технология измерения сигналов
основана на быстрой оцифровке входных сигналов и их обработке с помощью цифровых сигнальных процессоров (DSP).
Это позволяет существенно повысить быстродействие процедур сбора и обработки акустических сигналов, а также надежность функционирования аппаратуры. Кроме того, переход на современную элементную базу позволяет выполнить на одной плате от 2 до 4 каналов сбора АЭ-информации, что дает возможность увеличить количество каналов в одном корпусе аппаратуры.
Среди АЭ-систем, использующих описанную технологию измерения сигналов, следует отметить системы MISTRAS (PAC); AMS, AMSY.
- Регистрация волновой формы и анализ спектра акустических сигналов, основанные на использовании быстродействующих АЦП.
Это позволяет повысить информативность регистрируемой акустической информации, используя помимо традиционных параметров АЭ-сигналов (амплитуда, длительность, время нарастания переднего фронта, число осцилляций и др.) характеристики их волновой формы и полученного из нее быстрым Фурье-преобразованием спектрального состава.
Уже при разработке первых своих систем (SPARTAN, LOCAN) фирма РАС использовала регистрацию временной формы АЭ-импульсов с последующим получением спектра. Однако этот режим мог использоваться по ограниченному числу каналов, причем только в режиме пост-анализа, не связанного с общей зарегистрированной информацией. Последняя разработка этой фирмы - многоканальная система MISTRAS (рис. 1 ,а) - использует цифровую обработку с применением DSP для формирования традиционных параметров импульсов, но не предусматривает возможности для анализа в реальном масштабе времени волновых форм и спектров акустических сигналов в каждом канале приема.
Многоканальная система AMSY4 фирмы Valien Systeme (рис. 1,б) также позволяет регистрировать волновые формы сигналов, которые накапливаются в модуле сбора в буферах большой емкости (16 Мбайт в каждом канале) параллельно с регистрацией и анализом в реальном времени традиционных параметров импульсов. Детальный анализ зарегистрированных волновых форм осуществляется в режиме пост-анализа.
Можно сказать, что в упомянутых системах режим измерения волновой формы и анализа спектра возможен только как альтернативный основному режиму работы и используется в основном лишь для исследовательских целей или для выборочного контроля по небольшому числу каналов приема.
- Реальное время обработки больших потоков информации и оценки состояния объекта, т. е. непосредственно в процессе его нагружения.
Это особенно важно при пневмоиспытаниях сосудов давления, когда наряду с общей оценкой состояния объекта контроля необходимо обеспечить безопасность его испытаний. Эта задача может быть решена с использованием современных аппаратных и программных средств, адаптированных к особенностям метода АЭ.
Многолетний опыт ЦНИИ им. акад. А. Н. Крылова в использовании 32х-канальной системы SPARTAN, а также нескольких моделей аппаратуры спектрального анализа (СА-100, ЭМИС-1 и ЭМИС-2 разработки НПО "Дальстандарт", г. Хабаровск), как при экспериментальных исследованиях процессов зарождения и развития усталостных трещин в материалах и сварных соединениях опытных образцов и узлов в натурных толщинах, модельных и натурных испытаниях судостроительных корпусных оболочечных конструкций, так и при освидетельствованиях заводских сосудов давления и трубопроводов в различных отраслях промышленности позволил предложить концепцию АЭ-системы нового поколения МАЭС (рис. 2).
Рис. 2
МАЭС - система с сетевой многопроцессорной архитектурой, состоящая из модулей сбора и анализа, снабженных стандартными процессорами Intel. В качестве каналов приема использованы специально разработанные импульсные АЦП с полосой частот 2 МГц, отличающиеся тем, что они способны параллельно с оцифровкой акустических импульсов регистрировать их время прихода на приемный канал, используя для этого тактовую частоту оцифровки аналогового сигнала, синхронизированную по всем каналам системы, что необходимо и достаточно для определения координат источника АЭ на развертке контролируемой конструкции. Для реализации этой функциональной возможности модули сбора и анализа связаны сетевой магистралью ETHERNET и работают под управлением сетевой многозадачной операционной системы реального времени QNX (фирма Quantum Software Systems, Канада).
Одна из важных задач, решаемых в модулях сбора, состоит в том, чтобы резко уменьшить поток данных, передаваемых в модуль анализа. Эта задача решается с использованием отбраковки акустических помех по признаку "сигнал/помеха", получаемому после цифровой обработки формы импульса, и позволяет существенно разгрузить центральный процессор модуля анализа и, таким образом, совместить спектральный анализ в реальном масштабе времени с задачами статистического, локационного и критериального анализа.
На рис. 3.1 -3.3 приведены волновые формы и спектры некоторых АЭ-импульсов, излученных источниками-дефектами, и акустических помех, зарегистрированных системой МАЭС в ходе лабораторных исследований и промышленного АЭ-контроля. При этом использовались широкополосные ПАЭ типа WD фирмы РАС (частотный диапазон 100-1000 кГц).
Рис. 3. Волновые формы и спектры типичных АЭ-сигналов от дефектов (7 - 3) и сигналов акустических помех (4 - 6):
1 - от скачкообразно развивающейся поверхностной усталостной трещины полуэллиптической формы при ресурсных испытаниях крупногабаритной толстолистовой титановой сварной пластины на изгиб;
2 - при страгивании трещины прямолинейного фронта при испытаниях стального образца на коррозионную трещи- ностойкость;
3- от поверхностной микротрещины при пневмоиспыта- ниях автоклава;
4- типичный сигнал от трения в опорах гидравлической испытательной машины при ресурсных испытаниях на изгиб сварной толстолистовой титановой пластины;
5 - помеха, вызванная утечкой газа через фланцевое соединение реактора риформинга;
6- помеха, вызванная падением капли дождя при пнев- моиспытаниях ресивера сжатого воздуха.
На рис. 3.4 - 3.6 приведены характеристики акустических сигналов различной природы, относящихся к классу помех.
Очевидны различия волновых форм акустических помех (непрерывный сигнал) и сигналов АЭ-природы от трещин (дискретный сигнал с характерной крутизной нарастания переднего фронта до пиковой амплитуды и последующим резким снижением амплитуд по длительности сигнала). Спектральные мощности АЭ-сигналов отличаются ярко выраженным наличием высокочастотных гармоник (более 200 кГц). Исключение составляет близкая к дискретному импульсу форма сигнала от удара капли дождя (рис. 3.6), однако, спектр этого сигнала отличается от АЭ-сигналов отсутствием высокочастотных гармоник.
Рис. 4. Волновая форма акустических сигналов от помех (а) и дефектов (б) и алгоритм фильтрации помех
Рис. 4 иллюстрирует принцип фильтрации акустических помех (шума) по волновой форме сигнала. Волновая форма (рис. 4, а) типична для сигналов, регистрируемых при механическом трении, истечении газа или жидкости. Для нее характерно равномерное распределение амплитуды сигнала по длительности, т. е. практически непрерывная эмиссия в течение значительного (обычно несколько десятков миллисекунд) промежутка времени. Типичная волновая форма дискретного АЭ-импульса от трещины показана на рис. 4, б. Она отличается крутизной переднего фронта и резким спадом амплитуды по времени. В системе МАЭС введен параметр "уровень шума", характеризующий степень приближения сигнала к форме, типичной для импульса шума (рис. 4, а). Он вычисляется как отношение среднего уровня положительной огибающей сигнала к пиковой амплитуде и меняется от 0 (в случае дельта-функции) до 100 единиц (в случае непрерывного шума одного уровня). Численное значение этого параметра используется как одна из первых ступеней фильтрации помех в реальном масштабе времени.
Рис. 5. Идентификация дефекта по критерию высокочастотности спектра сигнала
Спектры сигналов, соответствующих рассмотренным волновым формам, приведены на рис. 5. Спектр импульса от трещины характеризуется наличием высокочастотных гармоник. В качестве критерия степени высокочастотности спектра использована частота в кГц, соответствующая последнему пересечению некоего уровня (в данном случае 0,3) нормированной спектральной функции ("уровень 0,3"). В приведенном примере значения этого параметра составляют соответственно 140 (для сигнала помехи) и 600 кГц (для АЭ-импульса от трещины).
Возможности фильтрации и критериального анализа акустической информации в реальном времени по волновым и частотным характеристикам весьма удачно были реализованы при контроле сварного титанового соединения непосредственно в процессе сварки. Регистрация сигналов осуществлялась широкополосными ПАЭ типа WD. Цель АЭ-контроля - выявление объемных окислений многопроходного сварного шва толстолистового титанового сплава, образующихся при нарушениях аргоновой защиты и являющихся источниками образования микротрещин уже в начальной фазе остывания шва. Процесс сварки сопровождается интенсивным излучением помех, обусловленных горением сварочной дуги, формированием сварочной ванны обдувом струей защитного газа аргона, скольжением защитных фартуков и горелки и другими источниками.
Рис. 6. Схема расположения дефектов в многопроходном сварном шве титанового сплава и результаты его АЭ-контроля в процессе сварки и остывания
На рис. 6 приведена гистограмма распределения активности АЭ по номерам проходов сварного шва. При образовании объемного окисления параметр активности АЭ возрастал примерно на порядок, что позволяло уверенно выявлять эти дефекты. Причем в случае пропуска дефекта активность АЭ из зарегистрированного источника надежно регистрировалась не менее чем на 6-7 последующих проходах.
На рис. 7 показан пример плоскостной локации источников акустических сигналов на развертке корпуса автоклава, зарегистрированных в процессе его пневмоиспытаний на АО "Красный треугольник". Один из наиболее сложных, но часто встречающихся случаев, когда источником акустических помех и АЭ-сигналов является один и тот же элемент конструкции. В данном случае такими элементами являлись подкладные пластины между горизонтально расположенным корпусом, к которому они приварены (источники АЭ-сигналов - дефекты в сварных швах), и неподвижными опорами, относительно которых перемещался корпус при его деформировании в процессе пневмонагружения, генерируя при этом интенсивные акустические помехи от трения-скольжения. В этом случае помимо неприменимости пространственной селекции сигналов, сложность фильтрации помех заключается и в том, что перемещение корпуса относительно опор, как дискретный процесс преодоления трения покоя, генерирует акустические помехи достаточно близкие по длительности и амплитуде к сигналам АЭ-природы и практически неразличимые при использовании резонансных ПАЭ. В таких случаях особенно эффективно использование анализа широкополосных сигналов со следующими критериями фильтрации:
- "уровень шума", как А ср /А макс > 30 - признак помехи;
- "уровень 0,3", как F03 > 400 - признак АЭ-сигнала.
В приведенном примере в результате применения фильтрации зарегистрированной информации по указанным критериям были выделены высокочастотные АЭ-сигналы, а в местах их источников магнитопорошковым методом были выявлены цепочки микротрещин протяженностью от 5 до 20 мм в сварных швах приварки подкладных пластин к корпусу автоклава.
Рис. 7. Плоскостная локация источников акустических сигналов на развертке корпуса автоклава
Уникальные возможности АЭ-метода были эффективно использованы для оценки активности трещин, выявленных в сварных швах приварки балок подвески противовеса к полотну поперечной балки металлоконструкции крыла разводного пролета моста Александра Невского. В этих наиболее напряженных районах конструкции при разведении-сведении крыльев пролета реализуется близкий к отнулевому цикл нагружения, причем с максимумом в наведенном состоянии. Информация записывалась системой МАЭС как в наведенном состоянии, при инициировании АЭ-излучения от трещин наложенной на максимальную статическую нагрузку высокочастотной составляющей от проходящего по мосту транспорта, так и в период цикла разведения-сведения пролета, когда нагрузка снижается до минимальной и опять поднимается до максимума. На рис. 8. приведены гистограммы распределения низкочастотных помех ("уровень 0,3" < 200 кГц) и высокочастотных АЭ-сигналов (сигналов от трещин), зарегистрированных при этих двух режимах нагружения. Очевидная акустическая активность трещин при реализации максимального размаха амплитуды приложенных напряжений в цикле разведения-сведения свидетельствует о том, что они являются развивающимися.
Заканчивая рассмотрение преимуществ использования широкополосных сигналов при идентификации дефектов, нельзя не отметить такое качество, как универсальность широкополосных ПАЭ. Такая важная характеристика, как дальность приема ПАЭ, определяющая необходимое число каналов, с дефицитом которых часто приходится сталкиваться при контроле крупногабаритных объектов, зависит от сочетания многих факторов: толщины материала, состояния его поверхности, наличия контакта с жидкостью или газом и пр. Сочетание этих факторов обусловливает, например, феномен "глухоты" на расстояниях свыше 2 м наиболее распространенных резонансных ПАЭ (частота 100-200 кГц) при гидравлических испытаниях тонкостенных сосудов (толщиной до 30 мм) и "слышимости" до 5 м более высокочастотными ПАЭ (частота 300^00 кГц), в то время как при пневматике картина изменяется на прямо противоположную. Это объясняется такими физическими эффектами, как разномодовость волн, связанная с толщиной стенки объекта, различие в коэффициентах затухания мод, изменение формы волны и частотного состава исходного сигнала (дисперсия скорости и затухания) и т. д., что является предметом специального рассмотрения. Однако как показывает практика, во всех случаях вариаций этих физических эффектов и механических факторов широкополосные ПАЭ оказываются более устойчивыми к ним, чем резонансные, т. е. более универсальными.
Рис. 8. Оценка степени активности (пассивности) трещин в металлоконструкции крыла разводного пролета моста