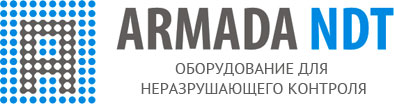
Ультразвуковой рельсовый дефектоскоп АДС-02
Об авторах
Воронов Николай Анатольевич
Генеральный директор ФГУП «Нижегородский завод им. М. В. Фрунзе», кандидат экономических наук.
Зябиров Хасян Шарафджанович
Первый вице-президент ОАО «Российские железные дороги», д-р техн. наук.
Кириллов Алексей Геннадьевич
Генеральный директор НТФ «Медуза».
Рейман Александр Михайлович
С. н. с. Института прикладной физики РАН, к. ф.-м. н.
Славинский Зиновий Михайлович
Д-р техн. наук
Шишков Александр Викторович
Главный инженер НТФ «Медуза».
Одной из причин аварий и крушений на железнодорожном транспорте являются изломы рельсов по дефектам в них. На сегодняшний день во всем мире наиболее надежным методом НК рельсов, уложенных в путь, является линейная многоракурсная ультразвуковая дефектоскопия. Другие методы НК применяются значительно реже из-за ограниченной номенклатуры выявляемых дефектов и чаще всего имеют сугубо научное, а не прикладное значение.
В диагностических службах железных дорог применяются как съемные (ультразвуковые дефектоскопы), так и мобильные (вагоны-дефектоскопы, автомотрисы) средства контроля. Выявление большей части (более 92 %) дефектов рельсов, уложенных в путь, и оперативное реагирование на факт обнаружения дефекта на сегодняшний день обеспечивается путем контроля рельсов ультразвуковыми съемными дефектоскопами. Вагоны-дефектоскопы и автомотрисы при кажущейся значительно большей производительности выдают заключение о подозрительном участке рельса с большой задержкой и требуют проведения вторичного контроля участков пути, вызывающих сомнения по показаниям мобильных средств.
Повышение требований к безопасности движения поездов требует перехода на качественно новый, более высокий уровень контроля, учитывающий достижения в области информационных технологий, замены устаревших приборов современными. На протяжении нескольких последних лет в России были разработаны и внедрены в практику съемные ультразвуковые рельсовые дефектоскопы нового поколения. С эксплуатационной точки зрения все эти приборы довольно близки, несмотря на многочисленные различия в конструктивной части и схемах прозвучивания рельсов.
Настоящая статья ставит своей целью не сравнение приборов (это задача для независимых и беспристрастных экспертов), а краткое изложение принципиальных особенностей автоматизированного дефектоскопа нового поколения АДС-02, разработанного сотрудниками Института прикладной физики РАН и НТФ «Медуза» совместно с Горьковской ж. д., производство которого организовано на ФГУП «Нижегородский завод им. М. В. Фрунзе».
До недавнего времени сплошная запись эхографической информации применялась только на мобильных средствах. На съемных дефектоскопах контроль за действиями операторов отсутствовал, информация об обнаруженных дефектах выдавалась лишь в виде звукового сигнала в наушники оператора и развертки типа А на экране прибора и нигде не фиксировалась. Даже применение усовершенствованных схем прозвучивания часто не приводило к повышению достоверности выявления дефекта из-за отрицательного действия субъективных факторов оператора.
Авторы статьи имеют многолетний опыт создания автоматизированных ультразвуковых комплексов различного применения (медицинского, технологического и т.п.), основанных на преимуществах совместного применения аппаратных и программных средств регистрации и обработки информации. Применение таких встраиваемых вычислительных систем позволяет минимизировать проблемно-ориентированную аппаратную часть и использовать все возможности современных технологий создания и модернизации программных оболочек. В 1999 г. впервые был представлен макет одной из возможных программно-аппаратурных реализаций ультразвукового съемного рельсового дефектоскопа АДС-02. За это время прибор прошел технические и эксплуатационные испытания, налажено его серийное производство, выпущена опытная партия. К настоящему времени накоплен немалый опыт эксплуатации дефектоскопа АДС-02 на железных дорогах России. Дефектоскоп имеет сертификаты Госстандарта РФ и МПС России и внесен в Реестр средств измерений, разрешенных к эксплуатации на сети федеральных железных дорог.
Основная задача, которую авторы ставили перед собой, - обеспечить сплошную запись информации, поступающей с эхографических каналов при работе в пути, и возможность ее оперативного просмотра. Для этого в программу, управляющую работой прибора, была встроена запись предварительно сжатой информации на твердотельный диск, входящий в состав прибора. Для упаковки был применен оригинальный алгоритм, разработанный сотрудником НТФ «Медуза» А. Б. Крупником. Этот алгоритм позволяет сжимать информацию без потерь со средним коэффициентом сжатия 10. Отметим, что за прошедшие 4 года емкость доступных твердотельных дисков увеличилась в десятки раз при одновременном снижении стоимости, что позволяет сейчас хранить на встроенном в прибор диске информацию о 50 - 100 км пройденного пути. Емкость диска определяется разумным соотношением «цена-объем», принципиальных ограничений для хранения записей о сотнях и тысячах километров нет.
Уже первые сравнительные испытания дефектоскопов, которые проводились в НИИ мостов МПС России в 2000 г., показали неоспоримые преимущества съемных дефектоскопов с регистрацией данных, поэтому комиссией было принято решение оснастить и другие типы дефектоскопов системами регистрации. Такие съемные регистраторы, подключаемые извне, были разработаны к приборам «РДМ-2» и «Авикон-01». Что же касается оперативного, в процессе контроля, просмотра эхограмм с разверткой типа В дефектоскоп АДС-02 до настоящего времени остается единственным прибором, предоставляющим такую возможность.
Аппаратная часть дефектоскопа АДС- 02 представляет собой 16-канальную приемо-передающую систему (по 7 независимых каналов на каждую нитку и канал ручных искателей). Схема про- звучивания, применяемая в настоящее время, соответствует схеме «Д» по классификации, и обеспечивает достаточно высокий уровень выявляемости дефектов (повышение условной технической эффективности примерно на 10 % при других вариантах схемы прозвучивания достигается значительным увеличением числа каналов контроля и, следовательно, усложнением аппаратуры). Следует отметить, что программная конфигурация искательной системы позволяет применять любую схему прозвучивания (до 8 каналов на одну нитку пути) путем создания и записи в память дефектоскопа файла описания искательной системы, в котором задаются углы ввода ультразвука в рельс и разворота относительно оси рельса, расположение преобразователей в лыже и порядок их поочередного возбуждения, а также ряд других параметров. Такая система позволяет также вносить в описание искателей не номинальные, а истинные значения углов ввода и поправок на задержку сигнала в протекторе искателя.
Принятые сигналы поступают на интерфейсную плату, где преобразуются в цифровой код и передаются во встроенный одноплатный компьютер. Одновременно в компьютер передается также информация о напряжении на аккумуляторе и внутренней температуре в приборе, а также текущая путейская координата от датчика, встроенного в одно из ведущих колес тележки. Вся дальнейшая обработка производится программным путем. В качестве встроенной вычислительной платформы в настоящее время применяется промышленный РС-совместимый компьютер Lippert с тактовой частотой 200 МГц и электролюминесцентный экран Planar с разрешением 320х240 точек. Управление режимами работы осуществляется с помощью герметичной 16-кнопочной клавиатуры. Все электронные компоненты прибора рассчитаны на применение в температурном диапазоне от -40° до +65° С.
В дефектоскопе АДС-02 применена двухуровневая регистрация дефектоскопической информации. Срабатывание звукового и светового индикаторов происходит при превышении сигналом опорного уровня по СО-3Р, а регистрация - по уровню - 4 дБ. Это позволяет наблюдать за подозрительными участками пути на «подпороговой» стадии развития дефекта. Заметим, что сама история появления этого режима демонстрирует преимущества программной реализации обработки сигналов. Режим был реализован и встроен в прибор без каких-либо изменений в аппаратной части в течение одного дня после того, как было принято решение о применении такого режима*
Информация запоминается в оперативной памяти прибора, сжимается и сохраняется на твердотельном диске. Следует отметить, что запись информации на диск производится независимо от желания оператора, эксплуатация дефектоскопа без регистратора (в отличие от систем со съемными регистраторами) невозможна. Кроме эхографической
информации фиксируются путейская координата, дата и время, действия оператора (изменение усиления, отключение каналов, нажатие кнопки «Стык» и т. п.), служебные отметки (режим «Блокнот»), а также эхограммы в виде А-разверток и М-разверток, полученные при перемещении ПЭП вручную.
Рис. 1. Вид экрана дефектоскопа: а - главное меню; б - режим сплошной записи; в - режим просмотра фрагментов; г - режим стоп-кадра
Просмотр информации возможен двумя способами. Во-первых, можно остановить запись и просмотреть всю записанную информацию на графическом экране прибора. В этом режиме можно перелистывать В-эхограмму постранично, перемещаться к выбранному фрагменту, проводить измерения с помощью курсора. Во-вторых, можно, не прерывая запись, просмотреть последний записанный участок (около 2 м, рис. 1). Такой режим стоп-кадра оказался особенно удачным при прохождении зоны болтового стыка, когда информация обрабатывается по особому алгоритму, и некоторые дефекты (например, кода 52) могут быть пропущены оператором, т. к. индикация не срабатывает. Опыт эксплуатации приборов на Горьковской ж. д. подтвердил эффективность этого режима.
Еще один режим, реализованный в приборе, - реконструкция условных изображений дефекта в проекции рельса (рис 2). Как показала практика, такая «подсказка» оператору полезна, и этот режим представления информации был в дальнейшем поддержан другими разработчиками.
Рис. 2. Проекция рельса с дефектами: а - на экране дефектоскопа, выполненная в пути до передачи информации в компьютер; б - полученная в программе углубленного анализа дефектограмм
Появление регистрирующей техники остро поставило вопрос об организации сбора и накопления информации о состоянии рельсов, уложенных в путь, в цехах дефектоскопии. Передача информации с дефектоскопа АДС-02 в стационарный компьютер сейчас может производиться двумя путями - через стандартный принтерный порт (LPT) и по сетевому протоколу, реализованному по спецификации Ethernet. Последний способ обеспечивает более чем десятикратное увеличение скорости обмена информацией между прибором и компьютером. Кроме того, с развитием сетевых технологий связана возможность организации удаленной передачи данных с приборов в цех дефектоскопии дистанции пути, которая сейчас находится в стадии разработки.
В комплект поставки дефектоскопа АДС-02 входит программная оболочка RAILTEST для Windows, разработанная сотрудниками НТФ «Медуза» С. Ю. Ксенофонтовым и А. В. Ерошиным. Она предназначена для приема информации с дефектоскопов типа АДС-02 по каналам LPT и Ethernet, просмотра и архивирования информации, печати фрагментов и протоколов. При этом можно использовать все преимущества современной компьютерной системы - высокое разрешение экрана, возможность работы с мышью, звук и т. п. (рис. 3). Хранение собранной информации ведется в папках, имена которых являются названиями участков контроля, а имена файлов - датами контроля. Таким образом, можно накапливать информацию о нескольких проходах по одному и тому же участку. Программа позволяет одновременно открыть и просматривать несколько файлов, листать журнал записи, быстро переходить от одного фрагмента к другому, увеличивать отдельный фрагмент, измерять глубины, а также реконструировать расположение условных изображений дефектов (аналогично функции реконструкции, реализованной в приборе). Программу можно использовать и для обучения операторов, так как в ней предусмотрена имитация звуковой и визуальной информации дефектоскопа АДС-02 при работе в пути, а также наглядные окна для трехмерной демонстрации хода ультразвукового луча и места расположения указателя (курсора В-развертки) в проекциях рельса.
Рис. 3.
Информация на компьютер записывается в формате, позволяющем передавать результаты контроля по коммуникационным каналам (электронной почте) в вышестоящие организации для анализа и хранения.
Внедрение дефектоскопов с регистраторами может привести и к еще одному качественно новому шагу - применению современных технологий автоматизированного распознавания растровых изображений для повышения производительности труда. Сейчас вся записанная информация просматривается вручную, что весьма утомительно, учитывая объем поступающей информации и возможности ошибок при визуальном распознавании эхограмм человеком. В настоящее время активно начинают применяться различные программы распознавания образов, например, на основе нейронных сетей, а эхограммы дефектов в виде В-развертки довольно легко алгоритмизируются. Запись эхографической информации в виде В-развертки («путейская координата - глубина рельса») позволяет легко сопоставлять данные, полученные от разных средств дефектоскопии. Применение новых информационных технологий может перевести ультразвуковую дефектоскопию рельсов на качественно новый уровень.
К настоящему времени серийное производство дефектоскопов АДС-02 освоило Федеральное унитарное предприятие - Нижегородский завод им. М. В. Фрунзе. Приборы успешно эксплуатируются службами дефектоскопии железных дорог РФ. Эффективность технических решений, реализованных в конструкции прибора, подтверждается результатами по выявлению дефектов (табл. 1). Один из приборов успешно применяется на РСП-17 (ГЖД) для входного контроля рельсов. Опыт эксплуатации партии дефектоскопов доказал правильность выбранного направления в разработке нового поколения систем НК - симбиоза программной гибкости и аппаратной надежности.
Табл. 1. Результаты эксплуатации дефектоскопов АДС-02 на Горьковской ж. д.
2002 г. |
10 месяцев 2003 г. |
|||||
Показатель |
Всех типов |
АДС-02 |
% к общему числу |
Всех типов |
АДС-02 |
% к общему числу |
Число съемных рельсовых дефектоскопов сплошного контроля |
263 |
7 |
2,66 |
274 |
17 |
6,2 |
Обнаружено ОДР, в том числе: |
3314 |
164 |
4,95 |
2886 |
223 |
7,7 |
на 1 прибор |
12,6 |
23,4 |
|
10,5 |
13,1 |
|
на 100 км пути |
1,12 |
3,05 |
|
1,14 |
2,5 |
|